Artworks discovered in archaeological sites showed that the history of pottery and ceramic existed from the prehistoric period as our early ancestors made similar earthenware objects with the most basic painted designs and crudely inscribed etchings and inscriptions.
As communal cultures evolved and basic but simple requirements of man increased, every culture began to develop their own individual creative expressions which resulted in an awesome array of artistic forms and features made from clay.
Different Types of Pottery and Ceramics
There are three different types of pottery and ceramics with each type essentially based on the physical properties of the clay they found within their region of abode. The three classifications are:
- Earthenware
- Porcelain
- China
1. Earthenware Pottery Made From Clay
Earthenware is made from almost any basic clay material that's often found at riverbeds. It can be shaped and moulded crudely with hand or turned on a potter’s wheel, hence its description as potter’s clay.
Earthenware can be fired at relatively low temperatures and if subjected to higher temperatures, it becomes harder and denser.
Clay colour depended on the geographical location of where it is found and the chemistry of each clay deposit, with natural colours varying from a pale washed-out tan to deep reds and brown shades. Like all ceramics, earthenware can be finished with glazing or left unglazed.
2. Porcelain
It is believed that authentic porcelain may have its roots in China. During the 9th century, it is claimed that China exported true porcelain to Mesopotamia.
However, the mastering of porcelain production was not achieved until the first decade of the 18th century at Meissen in Germany.
The material composition of porcelain is more complex than earthenware and is composed of kaolin and petuntse. Kaolin is a form of 'decayed' granite and is used in conjunction with petuntse, an equally decayed feldspathic rock.
Porcelain is fired at high temperatures by vitrifying the two components (kaolin and petuntse) to form an exceedingly hard and translucent clear white ceramic.
China Ceramics
China ceramics possess qualities of both earthenware and porcelain with opaque qualities, just like earthenware, but they are more resilient because of the inclusion of animal bone ash in its material components.
When compared to porcelain, China ceramics are not as strong and hard. This is due to the fact that they are fired with a less intense heat than is required for porcelain production.
China ceramics’ enhancing and decorative qualities are why they are commonly used in the making of everyday items like household tableware, beautiful dinner sets, and home décor items like urns, vases, figurines, etc… There are also water pots, planters, food platters, tea sets, medicine jars, and wine pitchers of old made from China pottery.
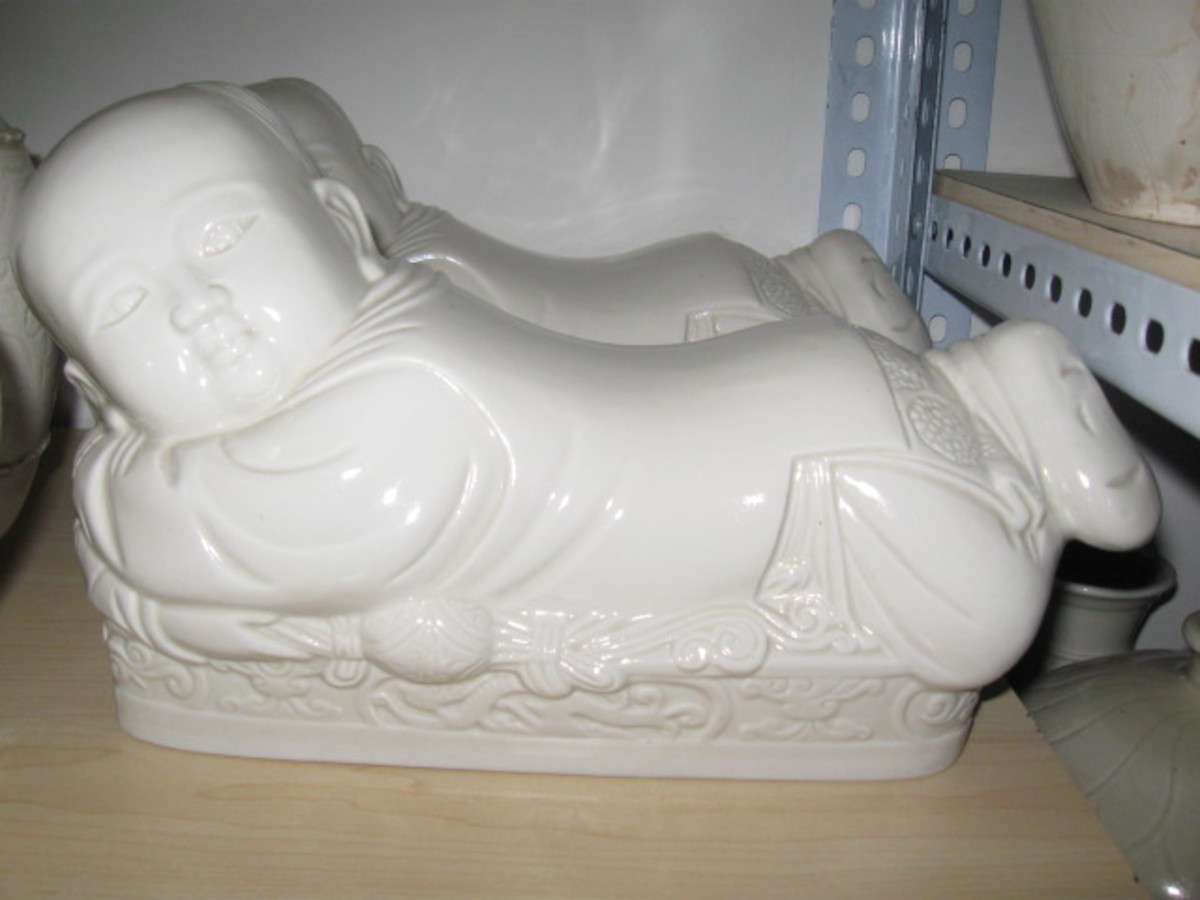
Early Italian Pottery
13th Century Majolica Pottery
The very early pieces of Italian ceramics date back to 9th century Mesopotamia and Baghdad, and by the 13th-century majolica was imported into Italy through the Isle of Majorca which was the main port for trading vessels sailing between Italy and Spain.
The name majolica apparently originated from the Isle of Majorca and was therefore called majolica by the Italians, not minding its source or origin. And shortly after the local Italian potters learnt the way of making ceramics, they began to create their own majolica, firstly by copying the Moorish Islamic designs, then eventually producing their own mix by adding their own ingredients.
14th Century Moorish Influence
The pottery of the early Renaissance in Italy was an elaboration of the majolica ware styles made by the Moors which the northern Italians started to copy in the 14th century. It is said that this Moorish influence on Italian ceramic art led to the great development of pottery designs which eventually evolved in 16th century Italy.
15th Century Medici Porcelain
The latter years of the 15th century saw an attempt at the production of porcelain in Venice, and by the beginning of the 16th century; the Medici family produced a mixture form that had translucent qualities, a form of porcelain also known as Medici porcelain.
The material was made into ewers, platters, and dishes, with patterns fashioned after art styles of the Renaissance and the Far East.
Today, very little of the Italian ceramic art of the 15th century can be found, but the pottery art of this period was what served as an inspiration for later ceramic makers in France, for their production of soft paste porcelain.
16th Century Themes and Forms
The great development in ceramics designs occurred in the early part of this century. Italian pottery works at the period were designed elaborately with beautiful hand painted finishes using bold strong colour patterns of festoons, foliage, scrolls, arabesques, dolphins, masks, cherubs, scriptural themes, scenes depicting historical subjects of the Roman Empire, and mythological themes.
The ceramic art forms included pitchers, urns, elaborate food platters, apothecary jars and pots of all shapes and sizes, vases and other typical household objects. Colours that was used on the majority of the majolica wares was black, orange shades, light blue, mulberry, and green.
18th Century Italian Potters
The influence of French and German styles of pottery became evident in 18th century Italy. Pottery works were founded in Venice as early as 1719, followed by Florence in 1735, Doccia in 1737, in two other locations in 1743 and 1771, Capo di Monte and Portico respectively, and finally in Naples in 1773.
Ancient Handmade Italian Ceramic Collector Items
Today, Italian ceramic art remains one of the most treasured collections of ancient pottery all over the art collector’s world.
These ancient art pieces are loved for their colourful designs and imaginative shapes and are no less admiring of the painstaking skill and attention to detail required in the production of such fine Italian ceramic ware.
Early Dutch Earthenware - Delft Pottery (Delftware)
When the Dutch began to master the art of making pottery, they established a ceramic production factory in the city of Delft.
The name of this ceramic production centre is the reason why over the centuries, Dutch ceramic art is referred to as Delftware, and this name eventually becomes one that is applied to all forms and styles of pottery and ceramics production from Holland.
Features of Delftware
Striking features of Delft ornamental and tableware include a heavy but brilliant glaze with notable blue colours (Delft blue) and decorations designed on a white background. Sketches used for their designs were conventional patterns, town and landscape scenes.
The patterns were painted prior to the glazing and firing of their ceramic ware. This process of ceramic decoration is known as under-glazing.
18th Century Imitation of Japanese and Chinese Ceramics
By the 18th century, the Dutch made a series of unsuccessful attempts to imitate the ceramic art styles of Japan and China but because of improvements in means of transportation, and the cheapness of Oriental wares which flooded the Dutch markets, they attained no great degree of success.
It was virtually impossible for them to compete with the costs of the cheaper products from the Far East. Their attempts at manufacturing porcelain were also futile, again for the same reasons.
England's Interest in Delft Pottery
During the early years of the century, Dutch ceramics or Delftware was exported to England because the collections were sought after by English collectors and wealthy homeowners.
Many of the ceramic pieces like drug pots and apothecary jars were used for commercial purposes by the medical practitioners of the time. Fireplace facings were adorned with small flat Dutch tiles, just as they were used for architectural purposes.
Eventually, in the cities of Bristol and Lambert, the English set up ceramic production factories and imitated Delftware ceramics.
Modern Dutch Ceramics
In modern times, most Delftware objects veer towards the tin-glaze tradition; they are almost always decorated in underglaze blue on a white clay background, with less use of tin glaze which happens to be a more expensive.
Today the words Delft Blue (or Delfts Blauw) has become a brand name and is hand painted on the underside of all authentic Dutch Delftware, a mark that collectors of genuine Dutch ceramic products look for.
French Ceramic Ware
16th Century - Bernard Palissy Pottery
Bernard Palissy is one of the greatest French craftsmen who was a bespoke potter and ceramic producer of the 16th century. He embarked on a series of experiments to find out how to produce unique and beautiful ceramic art.
He suffered much hardship and privation before finally discovering the production process and materials appropriate for the making of his now famous French ceramics. In the process, Palissy lost all his hard-earned savings to those experiments.
However, according to the history of bespoke craftsmen, it was only after he had in a fit of anger, burnt up his furniture in order to fuel his kiln that he finally succeeded in making the unique enamel mix for which French pottery is well noted for.
Influence of Italian Majolica Ware on French Ceramics
Palissy's work was strongly influenced by Italian ceramic ware. He had tried to imitate and improve its production process and was successful with his attempt.
This made him greatly inspired and he was soon modelling his forms and colouring largely from natural scenes, using plants, sea animals, crabs, fish, coral, seaweed, snakes, frogs, etc.., and these he always presented in a naturalistic manner.
He also used mythological and religious subjects occasionally for his designs and forms.
Value Placed on Palissy's Original Ceramics
The value placed on Palissy's original ceramic art ware is so high and this has made forgeries of his works flood the market.
To know his original pottery works, has a tint of reddish-yellow in the white areas, with the red tint of a poorer quality and their glazed finish are usually cracked.
Unfortunately, Bernard Palissy, who started off as a glass painter and later became the first great Renaissance ceramic potter, was eventually sent to prison for his embracing of Reformation principles.
Early English Ceramics
In the early 17th century, one of the most important developments in the art and style of pottery making occurred in England. Before then, pottery objects were crudely produced objects made strictly for practical uses.
There was no thought of making ceramics for decorative or appealing purposes.
Slipware
Most of the early English potteries were heavy earthenware pieces coated with a preliminary finish of a deep orange mix of water and clay known as slip. That’s how the name slipware came about.
Slipware ceramics were handmade, fired, and then coated with the slip mix. When the first layer of coating is dry, another layer of yellowish-white slip is applied after which the objects are glazed. Black and green slips were also used.
According to the common practice of pottery making at the time, earthenware was glazed with a galena lead oxide glaze that gave the finished product the distinguishing yellow tinge.
After glazing which most times showed touches of red and green, crudely sketched patterns were 'scratched' (called trailing) deeply onto the object’s surface with a sharp stick. The deep scratches brought out the first layer of slip, a deep orange tint.
Decorations always included the maker or owner's name, the date it was crafted, and a motto or some unique quote (or verse).
Other decorations etched on the ceramics include Fleur-de-lis (iris flower motifs), shields, rosettes, Coat of Arms, and grotesque figures of fanciful hybrid human, animal and plants.
Masters of Early English Pottery
Thomas Toft
He was the bespoke master of ornamental slipware in the 17th century.
Working in Burslem North Staffordshire, the centre for earthenware slipware, Thomas Toft’s style of pottery making, combined with the slip trailing method, was firmly established in the Staffordshire area by mid-1600.
He was famous for his slipware dishes, of which roughly 40 are still known to exist until this day. His pottery wares also include porringers, cooking containers, vessels, pots, bowls, cups, saucers, jars, basins, and candlesticks.
Josiah Wedgewood - Jasperware
A pottery maker who came to fame in 1759 when he inherited a pottery in Burslem. The history of early English pottery history will be incomplete without the mention of his Wedgwood ceramics, which is by far the most important name associated with the potteries of Staffordshire in England.
Ten years after his inheritance, he commenced production at his celebrated factory named "Etruria".
Wedgwood, a remarkable chemist and antiquarian, always sought how best to produce beautiful rare ceramic specimens of antique pottery art and was one of the first set of men to blend art and industry. He believed in employing the best talent available and was always willing to pay whatever it may cost.
His ceramics showed a classical influence of the Robert Adam art that spread over England, designing and producing pottery objects in styles that were in harmony with the furniture and décor styles of Adams.
Josiah Wedgwood's fame rose with the production of his famous Jasperware ceramics in the late 1700s. Its material is like a dull-white hard biscuit and it was easy to embellish and paint.
Its background came in blue, olive, black, sage or lilac and the embellishments were white Greek-style motifs or lovely figures wearing graceful robes.
Jasperware pieces include interior décor objects (displayed on shelves and free-standing cabinets) and tabletop ornaments. There were also jasperware mantels trims, door trims, knobs, and furniture appliqués. It was repeatedly used for appliqués in the designs of Sheraton and Hepplewhite furniture.
The Wedgewood name is still connected with English pottery production in Staffordshire, England.
Other famous potters - Ralph Simpson, Ralph Turner, William Taylor, and Richard Meir.
It is good to mention that by the end of the 17th century, English market was flooded with Oriental ceramics and Delftware. This paved the way for local potters to improve on their ceramic ware. They were influenced to create pottery styles similar to those produced by the Dutch, Chinese and Japanese.
And by the turn of the 18th century, the English potter was given over to large-scale experimentations and analysis of Oriental ceramics, because of the increased interest of the general public and ceramic art collectors in the porcelain ceramics of the Orients.
This in turn brought on many skilled sculptors and artists who became attracted to the rewarding business of ceramic production.
No comments:
Post a Comment